Timing screws, also known as feed screws, are the unsung heroes of efficient packaging lines. These precision-engineered tools not only guide containers seamlessly through packaging equipment but also perform a variety of essential functions to automate and optimize container position for packaging applications. Whether it’s feeding, orienting, turning, grouping, or even inverting containers, timing screws provide smooth operations and adaptability across diverse applications.
In this blog, we’ll explore the incredible versatility of timing screws and highlight 10 container types you might not have realized they can handle. From small, challenging shapes to complex configurations, discover how timing screws elevate your packaging equipment’s performance and flexibility.
1. Caps
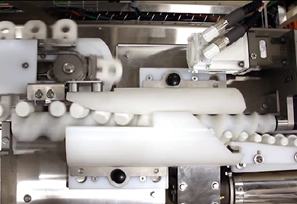
This timing screw driven solution efficiently handles small caps, starting with a 180-degree inversion using a timing screw and CNC-machined twist to expose the base for labeling. The inverted caps are guided to the labeling head via synchronized guiderails and a lug chain, keeping the base fully accessible for accurate label placement.
After labeling, the caps are laid down 90 degrees and fed into the flow wrapper lug chain for final packaging. With two labeling heads, the system maintains continuous operation, minimizing the risk of downtime. This solution highlights how timing screws handle small, intricate containers with precision.
2. Shot Bottles (50 mL Bottles)
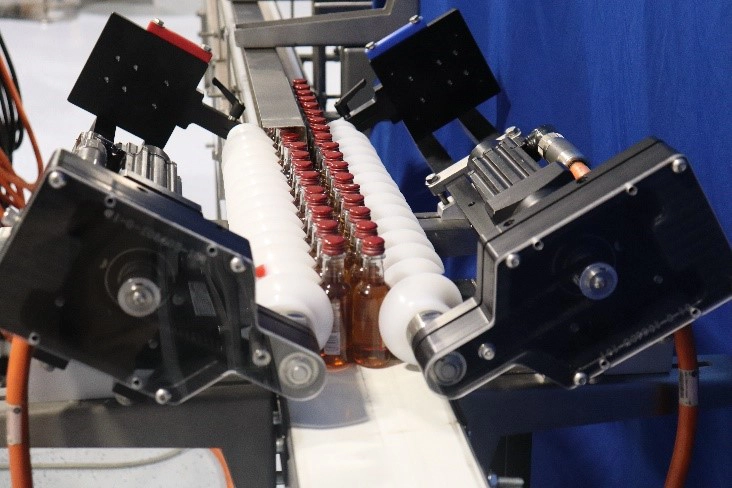
This custom solution organizes a single file of 50 mL containers into a 2×5 configuration, creating 10-packs with precision. Using timing screws, the system divides and indexes the containers while maintaining a 6-inch space between each pack. The spacing is carefully adjusted based on conveyor speed and screw modulation, delivering consistent results.
Additional options, such as guarding, conveyors, and controls, can be included to further tailor the system to specific needs. This application demonstrates how timing screws offer flexibility and accuracy in creating complex pack configurations.
3. Single Serve Coffee Pods
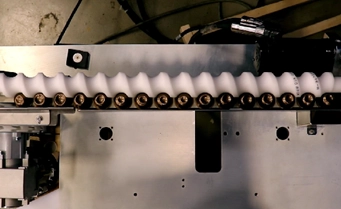
This system is designed to manage a single lane of tapered single serve coffee pods that require precise metering and indexing before reaching a vacuum gripper. Morrison’s solution utilizes a timing screw to regulate the flow, allowing the coffee pods to be perfectly spaced and positioned for seamless transfer.
This application showcases how timing screws can deliver accurate control and efficiency, even with small, delicate containers like coffee pods. By optimizing the process, the system enhances the downstream operation’s reliability and productivity.
4. Lip Balm
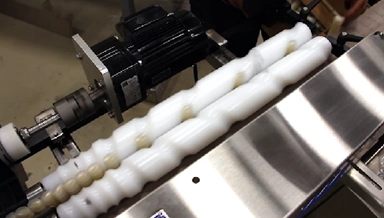
For oval lip balm containers, precision is key. Our dual timing screw system is designed to “square” these small containers for seamless feeding into your labeler. Due to the tight tolerances required, the containers are carefully positioned on the flat sections of conveyor cleats or links.
Synchronization is critical for this application, with all components—timing screws, top hold-downs, and conveyors—electrically connected through Nita-supplied servo motors. This alignment provides smooth, accurate handling of these small, delicate containers, preparing them perfectly for labeling.
This solution showcases how timing screws can tackle challenging container shapes with precision and reliability.
5. Alcohol Drink Pods
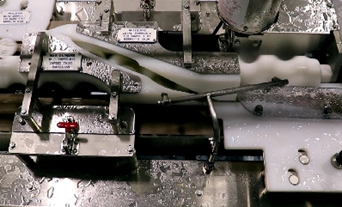
This application involves a single lane of liquid-filled, foil-sealed containers that require inversion from foil side down to foil side up. Morrison’s solution features a custom timing screw system designed to smoothly invert the containers, preparing them for downstream operations.
By leveraging the precision of timing screws, this system maintains product stability during inversion, providing an efficient and reliable process for managing delicate, foil-sealed containers.
6. Pharmaceutical Vials
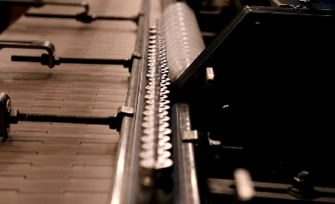
For metal containers requiring consistent 75mm spacing to function with a vision machine, Morrison provided a custom solution. Using a single screw drive unit, the containers are precisely spaced to the desired pitch, providing smooth and accurate integration with the vision system.
This simple yet effective solution demonstrates how timing screws can be tailored to meet specific requirements, enhancing efficiency and precision in container handling.
7. Mini Hand Sanitizer
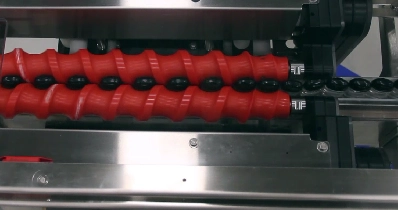
When dealing with a single lane of oval containers requiring consistent spacing before labeling, our dual timing screw system provides the perfect solution. This system meters containers with precision, feeding them into the labeler’s top hold-down belt at consistent intervals.
By positively handling each container and discharging them parallel to the flow, the dual screws provide accurate and efficient label placement. This approach highlights the versatility of timing screws in managing unique container shapes like ovals while maintaining smooth, reliable operations.
Timing screws may be small, but they are the backbone of efficient packaging operations. Whether handling delicate pharmaceutical vials or complex configurations like alcohol drink pods and coffee pods, their precision and adaptability make them essential for seamless container movement. By controlling metering, orienting, spacing, and inverting, timing screws synchronize packaging processes, keeping lines running smoothly and minimizing downtime. As you assess your production line, think of timing screws as the automation workhorse—driving efficiency, maintaining consistency, and tackling even the most challenging container designs with ease.
Contact us to learn more about timing screws today!