Glenwood, IL – In response to a growing need to automate as many parts of the production process as possible, Morrison Container Handling Solutions launches its new Model 20 Can Opener, a scalable counterpart to its successful Model 60 Can Opener that increase bulk food production capabilities.
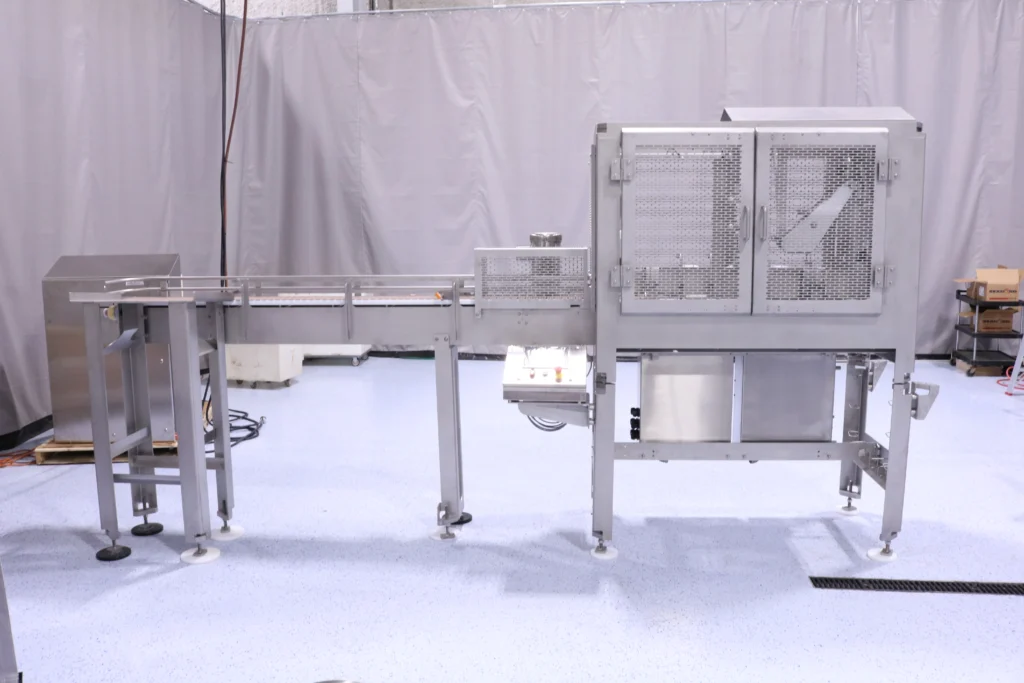
Food processors and manufacturers that rely on bulk #10 cans for ingredient preparation face numerous operational challenges, including labor shortages, safety concerns, and slow, inefficient manual processes. The Model 20 Automated Can Opener alleviates these issues by providing a streamlined, automated solution that improves productivity while reducing labor constraints. This is a great option if the Model 60 opener is more robust than needed for this application.
“With an increasing need to remove human labor from interacting with food products during production, our industrial can openers have seen more interest than ever before,” President Chris Wilson said. “We were routinely asked if we had a reduced footprint system in order to accommodate scaling operations, and we wanted to provide that solution.”
The Model 20 Can Opener opens #10 cans at a speed of 20 cans per minute. Cans enter the system via a loading table, metered by a timing screw for control while a crown punch opens the cans. Each lid is de-lidded with a magnetic de-lidder, safely discharging them into a chute. Opened cans continue via a discharge conveyor for an operator to dump.
“It’s our goal at Morrison to design equipment that can be modified as our customers grow or their products change, so when the opportunity to expand our can opener offerings can up, we wanted to take the same approach,” Vice President of Engineering Ryan Finke said. “What we love about the Model 20 is it is the best of the Model 60, scaled down, and it can easily be scaled up to add in automated dump and can crushing as the customer expands their capacity needs, all within the same machine, maximizing investment for our customers while minimizing costs.”
A Scalable Automation Solution
The Model 20 Automated Can Opener is designed for companies looking to take the first step in automating their can opening processes without fully transitioning to a completely automated system. Its modular design allows for future upgrades, including product dumping, rinsing, and crushing capabilities, making it an adaptable solution for growing businesses.
Key features of the Model 20 include:
- Automated Efficiency: Opens up to 20 cans per minute, significantly reducing manual labor.
- Safety Guarding: Perimeter guarding and automatic system shutdown protect operators from potential injuries.
- Scalability: Can be enhanced with additional automation modules as production needs grow.
- Durability and Compliance: Made with high-washdown stainless steel construction for long-term use in food production environments.
- Flexible Configurations: Compatible with different conveyor layouts, product dump bins, and product viscosity requirements.
“The launch of the Model 20 is a game-changer for food processors who need a more efficient and scalable approach to their can opening process,” CEO Nancy Wilson said. “With the ability to open up to 20 cans per minute, this system not only increases throughput but also helps enhance worker safety and allows companies to repurpose labor to other essential tasks.”
For customers with larger operations the Model 60 Can Opener is a perfect fit. The all-in-one machine opens, de-lids, dumps, cleans, and crushes the cans at a rate of 60 cans per minute. For information on which model is right for your operation and pricing, please visit www.morrison-chs.com. View a demo video of the full system in action here.
ABOUT MORRISON CONTAINER HANDLING SOLUTIONS
Since 1971, Morrison Container Handling Solutions has prided itself on providing the best solutions in container handling and is excited to mark this momentous occasion in its history.
Founded by President Nick Wilson, Morrison Container Handling Solutions is well known in the packaging industry for developing customer-focused, simple and innovative solutions for container handling needs. The company was started by Wilson to provide superior bottle handling parts and timing screws and has now grown to be recognized as the source for innovative container-focused handling solutions, even for the most difficult rigid or semi-rigid containers. Since its inception, Morrison has provided solutions for companies within the United States and internationally. Morrison is well-known industry-wide for attentive service to a wide variety of customers’ container handling needs – always with Support Built In®, the company’s promise to deliver quality products and support them 24/7, from initial concept to years after installation.
Continuing the legacy Nick’s son, Chris Wilson, has been with Morrison for more than 30 years and is now President. In 2011, Nick recruited his wife, Nancy Wilson, to bring her 25 years of Ford Motor Company corporate marketing and leadership experience to the team. In 2013, Nancy became owner and CEO of Morrison and oversees daily operations.